How padel rackets are made: A look inside the manufacturing process
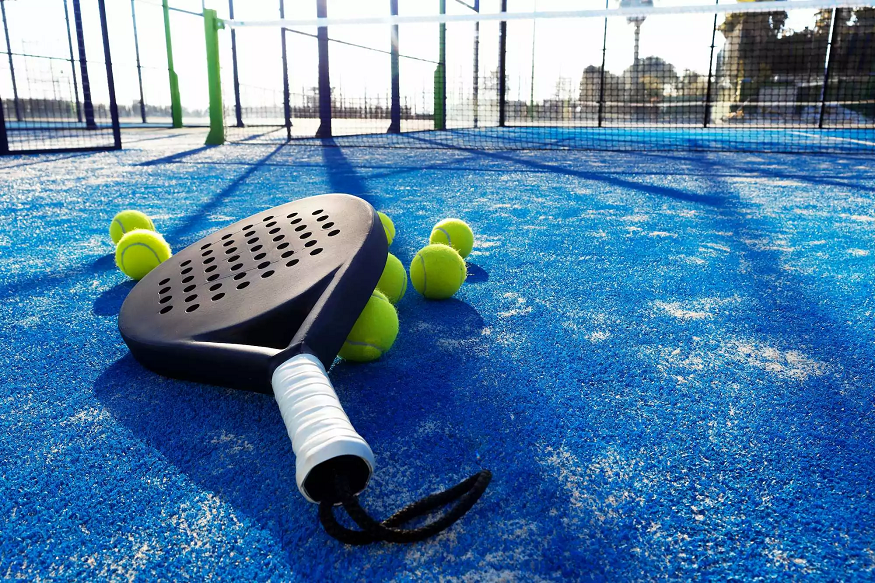
The padel racket manufacturing process is a finely tuned, multi step process with an emphasis on precision and high performance materials. From selecting quality composites to final assembly, each step is carefully executed to produce composites with optimal durability, control, and performance. In this article we’ll take a look inside the technical workflow behind padel rackets, and see how they are made.
Raw Material Selection
Sourcing high grade materials for padel rackets is the first step in padel racket production by manufacturer. For their strength to weight ratio and flexibility, they choose composite blends of carbon fiber and fiberglass fabrics. These fabric layers are bound together by polymeric resins, usually epoxy or polyester, to form a rigid, but responsive structure. Density is selected to balance power and control for foam cores, usually EVA or PE. Protective external coverings and metal inserts for handle reinforcement and straightforward grip installations are also procured. To ensure material consistency, tensile strength and resin viscosity are verified through supplier audits and batch testing. The result is a thorough evaluation of composite fabrics, core foams and supplemental components, which provide the foundation for racket durability. Manufacturers control raw material quality to reduce defects and produce rackets with predictable feel and performance characteristics in subsequent production stages. In addition, material choices are influenced by environmental considerations to meet broad sustainability standards.
Molding and shaping
Once raw materials are approved, fabric layers and core foams are arranged in precision molds that precisely determine the shape and weight distribution of the racket. Carbon or fiberglass fabrics pre-impregnated with resin are stacked in accordance with the engineering specifications and core materials are inserted into the central cavity. Manual layup can be used to fine tune fiber orientation, while automated layup systems can position layers with minimal error. The mold halves are then assembled and placed under heat and pressure in hydraulic presses or autoclaves for curing and resin flow. To prevent voids, temperature profiles are controlled to fully polymer crosslink. After curing, the molded blank includes air holes and design contours as well as handle geometry. The part is then de-molded by skilled operators who examine it for surface defects and continue. Raw components are transformed into solid, dimensionally accurate racket blanks for reinforcement and finishing during this stage. Mold settings are strictly recorded in production documentation for traceability.
Reinforcement and core
Racket blanks are reinforced after initial molding to optimize stiffness and weight distribution. The technicians drill precise air holes in the blade, reducing weight and increasing aerodynamics without sacrificing structural integrity. Foam inserts can be bonded to increase vibration dampening, and core edges can be trimmed and sanded to exact dimensions. The high stress areas can be manually applied with Kevlar or aramid fiber strips, while the handle junction is reinforced with carbon fiber patches. These layers are secured with epoxy adhesives and pressurized using clamps during secondary curing cycles. Adhesive performance is ensured to be consistent through temperature controlled ovens. After reinforcement, the core (which is typically an EVA or PE foam) is evaluated for density and uniformity. Localized sanding or filling corrects any irregularities. Regular ultrasonic inspections are also performed by technicians and physical testing to confirm mechanical properties and internal bonding. The very process of this meticulous reinforcement ensures that each racket has the targeted flex characteristics and durability before surface treatments are applied.
Surface treatment
Once core reinforcement is complete, the racket blank moves to surface treatment to make the racket more durable and aesthetically appealing. Mold lines and air hole edges are smoothed out with fine sanding operators. It promotes adhesion of decorative film and paint by applying a primer layer. Graphics and alignment guides are added, including crossover patterns and weight indicators, through silk screening or rotary printing. The surface is protected by clear coats of polyurethane or polyester lacquer against abrasion and UV exposure. Automated spray booths regulate application thickness and ambient conditions between each coat. Surface irregularities are removed in final polishing and the reflectivity is guaranteed to be consistent. In regions focused on the development of padel tennis, such as in micro etching of specific textures to enhance ball spin and grip. This comprehensive surface process ensures racket longevity, maintains design precision, and preps each blank for handle incorporation. Before packaging blanks, finish integrity is confirmed by inspectors through careful visual reviews and gloss and thickness measurements.
Quality control
Finished blanks are evaluated by quality control teams through a series of mechanical and dimensional tests to verify performance standards. Overall weight is verified to within tight tolerances by precision scales, and thickness and handle dimensions are measured with calipers. Frame resilience is assessed using impact tests that simulate real world ball strikes. Moisture analysis ensures core materials stay within safe humidity ranges. Peel tests are used to test surface adhesion. Environmental conditions are also monitored at facilities padel racket manufacturing in Dubai, in order to simulate local temperature and humidity during testing. Internal voids are detected with ultrasonic inspections, and ball return characteristics are measured with rebound machines. Parts that fail any criteria are sent back for remediation or recycling. Test results and batch identification are documented in detailed inspection reports that are traceable throughout production. This rigorous quality control protocol ensures consistency and reliability across racket batches. Fatigue tests replicate thousands of swings to validate endurance, and chemical tests confirm sweat resistant coatings.
Final assembly and packaging
Bonding of the handle components (composite extension and ergonomic end cap) initiates final assembly. These parts are secured with thermo bonded adhesives before a decorative grip tap is applied. Uniform tension grips are wrapped around for consistent feel and moisture management. Protective bumpers or edge tape are installed around the frame perimeter to protect it from impact damage. Authenticity and regulatory compliance are ensured by affixing serial numbers and certification labels. After that, rackets are completed and then go into protective sleeves or rigid packaging, with foam inserts to prevent movement during transit. Specification details like weight, balance point, and flex rating are included on the packaging labels. Barcode scanning helps warehouse staff to organize batched units by size and destination. Pallets are boxed, ready for shipping by road, sea or air freight, to ensure rackets get to distributors and retailers in the best condition possible, helping to improve overall customer satisfaction and loyalty.
Looking at every step of padel racket production, one can marvel at the combined importance of material science, precision molding, and skilled craftsmanship. Consistency, safety and performance is achieved through quality assurance. Rackets undergo surface finishes and final inspections for play. The depth of design and engineering and how it comes together to deliver a high quality racket is appreciated by appreciating the complexity of this manufacturing journey.